Cylindrical rollers wrapped in a layer of the elastomer substance polyurethane are known as polyurethane rollers. Depending on the use, the inner roller core is vulnerable to dents, corrosion, scratches, and other damage. The inner roller core’s polyurethane layer includes built-in qualities, impact strength, and abrasion resistance. The most common elastomer used for rollers is polyurethane. From various types and ratios of compounding materials, a variety of blends can be created. Different mechanical qualities can be obtained through blending to meet the needs of a certain purpose. Its most attractive characteristics are its toughness, high impingement resistance, shock absorption, and fatigue resistance. Read More…
Harwood Rubber Products provides top quality rubber rollers and a variety of custom products. We are capable of producing a great diversity of rolls and coverings for a broad customer base.
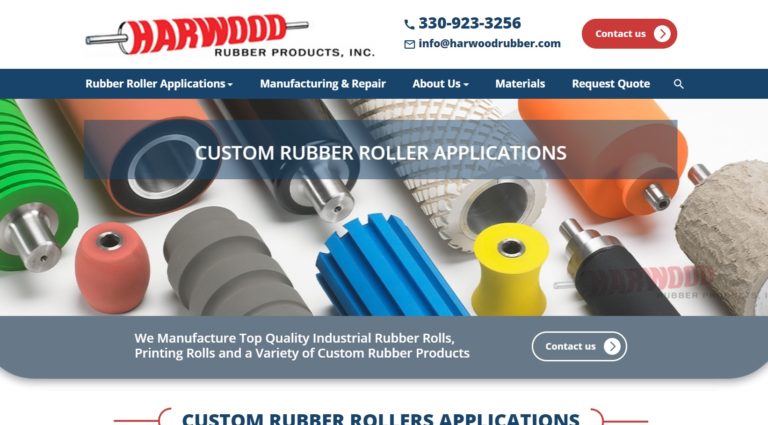
Since 1948, REDCO Rubber Engineering & Development has been manufacturing rubber rollers, idler rolls and conveyor rollers. We serve industries such as computers, printers and paper handling.
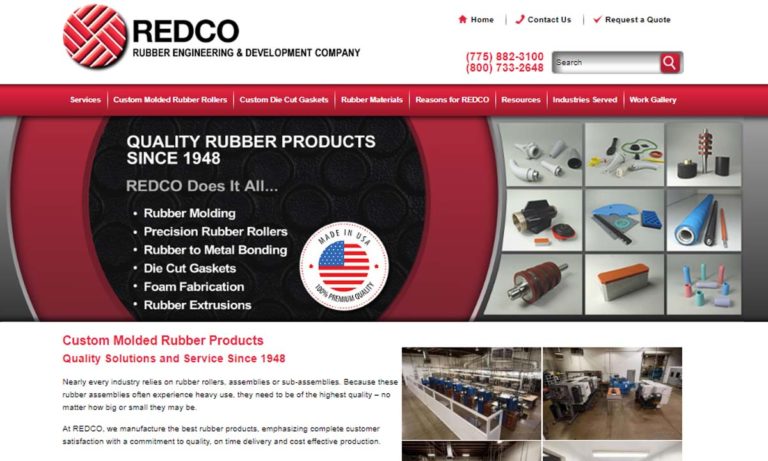
Our guide rollers are made from the highest quality materials in the industry. We take pride in adhering to our company values, like integrity and honesty. As a family owned and operated company, we like to treat customers like our own family. We will always look for the best prices and the prefect solution. Give us a call today to see how we can help you meet your goals!
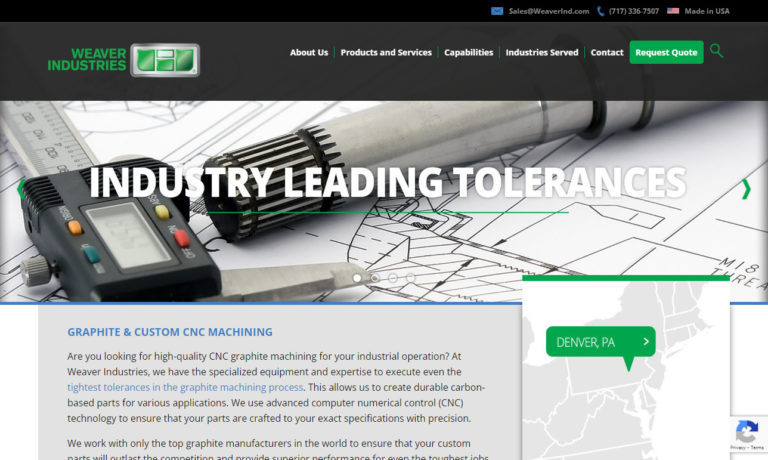
TPC, Inc. is a dedicated and trusted manufacturer of rollers. We manufacture rollers in all shapes, sizes, designs, and colors to meet the needs of our customers and keep their process moving. Our team of experts is dedicated to the production and innovation of our products. As a result, TPC, Inc.’s custom-fit solutions are perfected for customers of all industries.
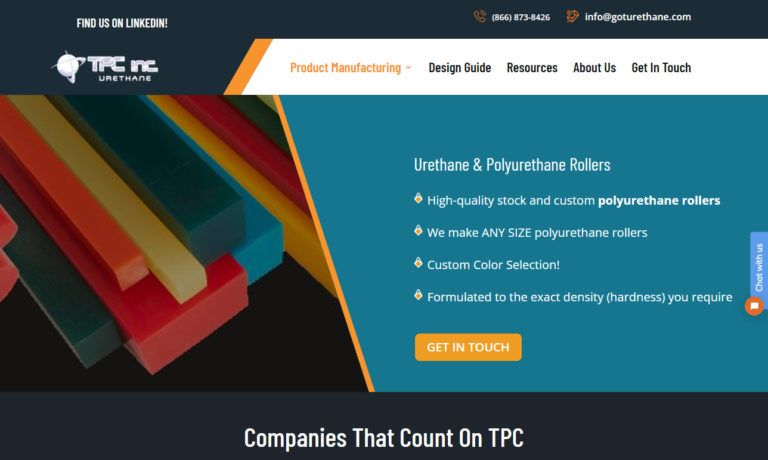
More Polyurethane Roller Manufacturers
Manufacturing Process of Polyurethane Rollers
Steel is the most typical material used in fabricating and preparing roller cores. A combination of sheet rolling, milling, cutting, and welding creates steel roller cores. The exterior cylinder, which contains polyurethane, is the major component. It is primarily created through rolling, and welding operations at steel mills, providing feedstock materials to polyurethane rollers' producers. A solid core or keyway and space for bearings, intended for one or both ends of the roller, are features of polyurethane rollers. Bearings lessen friction between the spinning and stationary components. The roller's design may impact the configuration, mounting, and bearing.
Cross-links are made between the chained molecules of elastomer compounds during the curing process. This increases the rubber's stability and improves its ability to withstand heat, cold, and solvents. The curing process involves heating the system, which starts bonding the curative chemicals. Some polyurethane polymer systems allow for ambient temperature curing. The polyurethane is heated and then cooled for a few minutes or several hours to cure. The polyurethane roller is subsequently cooled and removed from the mold. Another curing method used by other polyurethane systems is post-curing. The cast's mechanical qualities and thermal resistance are both enhanced by post-curing. The cast polyurethane rollers' surface is smoothed during the machining process by cutting away flashings and projecting regions. The conventional method involves grinding, which is accomplished by rolling a polyurethane roller against an abrasive wheel. Additional machining techniques, such as cutting and laser engraving, may be used to create surfaces with personalized profiles.

Advantages of Polyurethane Rollers
- Liquid Tolerance: Polyurethane can tolerate liquids like water and oils, as well as other petroleum-based solvents, depending on the type of polymer system utilized. Water resistance is necessary for rollers in situations with regular washdown or under wet service. Handling hydrocarbon-based solvents or chemicals, such as inks, requires oil resistance.
- Easy to Process: It is optional to use expensive or specialized machinery to process polyurethane. For example, an easy mixing process could require a batch mixer (no heating equipment needed). Other rubbers, on the other hand, use mastication and heating equipment.
- No Carbon Black Residue: Carbon black is frequently used as filler and reinforcement in rubber roller linings. However, applications like completed goods handling and printing can create unpleasant marks when rolled against a surface with enough force. Since polyurethane rollers don't employ carbon black, they don't have this issue.
Applications of Polyurethane Rollers
- Sturdy and Resilient: Industrial polyurethane-coated casters are hardy, resilient, sturdy, and able to support up to five tons type of caster. They are built of high-density thick polyurethane and have a greater capacity than rubber wheels. The fact that these polyurethane casters can transport extremely big loads without endangering floors or other surfaces is why they were chosen.
- Quiet and Unobtrusive: Industrial polyurethane casters work quietly and have a bigger footprint, lessening the floor's stress, similar to polyurethane rollers used on conveying systems.
- Long Lifespan: The flexibility of polyurethane industrial casters, which offers ergonomic advantages, accounts for their long lifespan.
- Resistance and Effectiveness: Conveyor rollers made of polyurethane are preferred because of their noise reduction, abrasion resistance, and solvent resistance. Conveying systems are the cornerstone of effective and seamless operations in packaging and shipping. Rapid material movement is required without damage or improper handling.
- Noise Suppression: Rollers made of polyurethane play a significant role in quickly moving equipment, tools, parts, and customer orders. Their noise-suppression abilities help to keep the workplace stress-free for employees.
- Idle and Return Rollers: Idler rollers, which serve various purposes to aid in the flow of items along a conveying belt, are a crucial component of a conveyor roller system. The conveying belt is supported by return rollers, one of the two idler rollers. Carrying rollers move materials, whereas return rollers support the conveying belt on its return.
Choosing the Proper Polyurethane Roller Manufacturer
To make sure you have the most productive outcome when purchasing polyurethane rollers from a polyurethane roller manufacturer, it is important to compare at least 4 manufacturers using our polyurethane roller directory. Each polyurethane roller manufacturer has a business profile page that highlights their areas of experience and capabilities and a contact form to directly communicate with the manufacturer for more information or request a quote. Review each polyurethane roller business website using our proprietary website previewer to get an idea of what each business specializes in, and then use our simple RFQ form to contact multiple polyurethane roller businesses with the same quote.